Quality 4.0: Transforming Quality Management in Industry 4.0
12/1/20248 min read
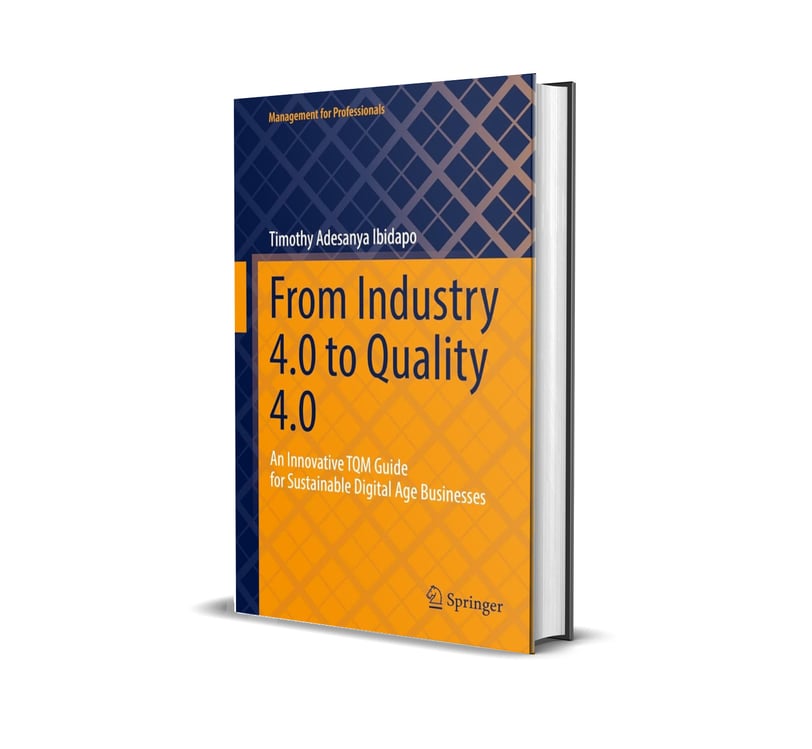
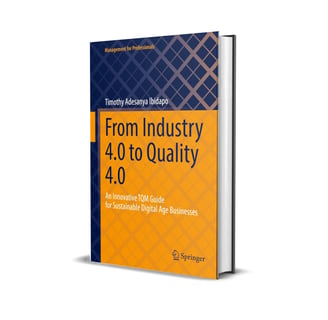
Introduction to Quality 4.0
Quality 4.0 represents a significant evolution in the landscape of quality management, emerging concurrently with the broader framework of Industry 4.0 and the ongoing digital transformation within various sectors. The term encapsulates the fusion of traditional quality principles with cutting-edge technologies, paving the way for enhanced operational efficiency. Organizations are increasingly recognizing the importance of integrating established quality methodologies, such as Total Quality Management (TQM) and Lean Manufacturing, with digital tools like big data analytics, artificial intelligence, and the Internet of Things (IoT).
The foundation of Quality 4.0 can be traced back to the need for a more agile and responsive approach to quality management, driven by the rapid advancements in technology. In this digital age, businesses are inundated with vast amounts of data, necessitating sophisticated analytical capabilities to draw actionable insights. Quality 4.0 leverages this data to monitor and improve processes in real time, thus ensuring that quality is not merely a post-production check, but an integral part of the product lifecycle from conception to delivery.
Traditional quality approaches often operated in isolation, lacking the dynamic feedback loops essential for rapid improvement. Quality 4.0 bridges this gap, facilitating a holistic view of quality across the entire organization. By integrating quality management into daily operations, companies can enhance customer satisfaction, streamline processes, and reduce costs. Furthermore, incorporating digital technologies allows organizations to predict and prevent quality issues proactively, transforming quality management from a reactive to a proactive discipline.
This seamless interface between traditional quality methods and modern digital innovations positions businesses to thrive in an increasingly competitive environment. As organizations embark on their Quality 4.0 journey, they will discover that the convergence of quality management and digital transformation is key to not only surviving but excelling in the fast-paced digital landscape.
The Role of Digital Technologies in Quality 4.0
In the advent of Quality 4.0, digital technologies play a pivotal role in transforming traditional quality management practices. These technologies, including Artificial Intelligence (AI), Machine Learning (ML), the Internet of Things (IoT), and Big Data Analytics, are reshaping how businesses approach quality assurance and control. A core component of this revolution lies in the ability of these digital tools to facilitate real-time data collection, monitoring, and analysis, which are critical for enhancing quality management processes.
Artificial Intelligence and Machine Learning are crucial in analyzing vast amounts of data generated by manufacturing processes. These technologies can identify patterns and anomalies that may not be visible to the human eye, allowing for predictive maintenance and enhancing product quality before it reaches the consumer. By leveraging AI and ML algorithms, organizations can automate quality checks, drastically reducing the time spent on manual inspections and minimizing the risk of human error.
The Internet of Things (IoT) further enhances quality management by connecting machines, devices, and sensors within the production environment. This interconnected network allows for continuous monitoring of equipment and products, providing instant feedback on performance metrics. With IoT, issues can be detected and addressed in real-time, fostering a proactive approach to quality assurance and reducing the occurrence of defects.
Big Data Analytics complements these technologies by enabling organizations to analyze structured and unstructured data from diverse sources. This capability enhances decision-making, as data-driven insights can inform quality strategies and operational improvements. Organizations can utilize Big Data to understand consumer preferences, track product performance, and optimize processes, ultimately leading to improved quality outcomes.
By integrating these digital technologies, businesses are not only enhancing their quality management practices but also creating a culture of continuous improvement and innovation in the digital era.
Key Components of Quality 4.0
Quality 4.0 represents a significant shift in how organizations approach quality management, integrating advanced technologies to enhance processes and outcomes. Among its critical components, digital twins, cyber-physical systems (CPS), and cloud computing stand out as transformative elements that facilitate this transition.
Digital twins are virtual replicas of physical assets, processes, or systems. By simulating real-time behavior, they allow managers to analyze performance, predict outcomes, and identify potential inefficiencies before they occur. This proactive approach aids in optimizing manufacturing processes by enabling informed decision-making and fostering continuous improvement. A digital twin facilitates scenario testing, allowing businesses to experiment with various strategies without the risk associated with physical trials. As a result, organizations enhance their quality management processes and reduce costs associated with defects and downtime.
Cyber-physical systems (CPS) further enhance this landscape by merging the physical and virtual worlds. These systems incorporate smart sensors and IoT devices to monitor production systems and environmental conditions in real time. By utilizing CPS, manufacturers can gather extensive data that informs quality control and process adjustments. This leads to higher levels of automation and precision in production, ultimately resulting in improved quality metrics. CPS serve as a backbone for predictive maintenance, where potential equipment failures can be addressed proactively, thus minimizing production interruptions and ensuring consistent quality.
Cloud computing plays a vital role in Quality 4.0 by providing the infrastructure necessary for data storage, processing, and analysis. The cloud enables organizations to access vast amounts of data from various sources and harness powerful analytics tools. This scalability facilitates collaboration among teams and partners, enhancing communication and improving responsiveness to market demands. By leveraging cloud technology, businesses can standardize quality management practices across different locations, ensuring a uniform approach to quality that aligns with industry standards.
Operational Excellence Through Quality 4.0
In the context of Quality 4.0, operational excellence is pursued through the integration of advanced technologies and data analytics. This modern approach employs methods such as predictive maintenance and smart manufacturing to enhance efficiency across various business operations. By leveraging the Internet of Things (IoT) and interconnected systems, organizations can monitor equipment conditions in real-time, allowing for the identification of potential failures before they occur. This proactive maintenance strategy not only minimizes downtime but also prolongs the lifecycle of critical assets, ensuring that operations remain uninterrupted and productive.
Smart manufacturing further amplifies operational excellence by utilizing advanced automation, robotics, and artificial intelligence. These technologies facilitate the creation of highly adaptable production environments that can respond swiftly to changing market demands. By employing data-driven insights, businesses can optimize production schedules, manage supply chains effectively, and deliver high-quality products consistently. The use of quality management systems that incorporate real-time data enables organizations to track performance metrics and identify areas for improvement, thus fostering a culture of continuous enhancement.
Moreover, the significant role of real-time data cannot be overstated in the pursuit of operational excellence through Quality 4.0. Organizations are increasingly empowered to collect and analyze vast amounts of data from various sources, leading to informed decision-making processes. This data-centric approach allows companies to quickly adapt to market trends and consumer preferences while maintaining strict quality standards. By harnessing analytics, businesses can uncover valuable insights that drive innovation and enhance competitive advantage.
In sum, Quality 4.0 serves as a catalyst for operational excellence by promoting advanced technologies, predictive strategies, and real-time analysis, all of which culminate in increased efficiency and superior product quality.
Customer-Centric Approaches in Quality 4.0
In the rapidly evolving landscape of Quality 4.0, customer-centricity stands out as a pivotal strategy for businesses aiming to thrive in the digital era. At the core of this approach lies the understanding that enhanced customer satisfaction is directly linked to quality improvements in both products and services. Businesses must embrace data analytics, which serves as a powerful tool in deciphering customer preferences and behaviors. By harnessing the wealth of data generated by modern technologies, organizations can gain valuable insights into customer needs, enabling a more tailored approach to product development.
Utilizing advanced analytics, companies can identify patterns, trends, and anomalies within customer interactions. This analysis not only informs product design but also informs service delivery, ensuring that customer expectations are not just met but exceeded. For instance, through the integration of machine learning and artificial intelligence, businesses can predict future customer needs and adapt their offerings accordingly. Such proactive measures are instrumental in fostering loyalty and driving repeat business, reinforcing the necessity for a customer-first mentality in Quality 4.0.
Moreover, engaging customers throughout their journey plays a crucial role in strengthening this relationship. Companies can implement feedback loops that solicit input at various stages, from initial design concepts to post-purchase evaluations. This iterative process not only demonstrates a commitment to customer voices but also allows businesses to make informed adjustments that enhance overall quality. As organizations adopt these customer-centric practices, they unlock opportunities for innovation and growth. By consistently prioritizing the customer perspective, businesses can ensure they remain competitive while delivering exceptional value in a dynamic marketplace.
Challenges and Considerations in Implementing Quality 4.0
As organizations strive to adopt Quality 4.0, they face a myriad of challenges that can impede progress. One of the primary obstacles is the inherent resistance to change within the workforce. Employees may be apprehensive about new technologies and the required shifts in operational processes, resulting in pushback that can hinder implementation efforts. Addressing this resistance requires effective communication and a comprehensive change management strategy, which can help foster buy-in and enthusiasm for the transition.
Another significant consideration is the necessity for employee training. Implementing Quality 4.0 technologies demands that staff are adequately equipped with the knowledge and skills to utilize these advanced systems effectively. As such, organizations must invest in training programs tailored to their specific needs, covering new tools like artificial intelligence, data analytics, and advanced manufacturing techniques. Continuous learning and support are crucial to ensure that employees feel confident and empowered in their new roles.
Cybersecurity concerns also pose a challenge to organizations embracing Quality 4.0. As digital technologies become more prevalent, the risk of cyber threats increases. Ensuring robust cybersecurity measures is imperative to protect sensitive data and maintain operational integrity. Organizations must evaluate their existing security frameworks and consider their relevance in the new digital landscape, implementing a proactive approach to safeguard against potential breaches.
Moreover, the integration of new technologies with existing systems can be complex, often requiring a thorough assessment of current infrastructures. Businesses must strategically plan for this integration to minimize disruptions to ongoing operations. Best practices suggest piloting new technologies in phased implementations to identify potential issues early on and ensuring that legacy systems can interface seamlessly with innovative solutions.
By acknowledging these challenges and implementing structured strategies, organizations can navigate the transition to Quality 4.0 more effectively and reap the benefits of enhanced efficiency and quality improvements.
The Future of Quality 4.0: Trends and Sustainability
The landscape of Quality 4.0 is rapidly evolving, shaped by emerging trends that intertwine technology, sustainability, and continuous improvement. As businesses navigate this digital era, the integration of advanced technologies like artificial intelligence (AI), machine learning, and the Internet of Things (IoT) becomes crucial. These tools not only optimize processes but also facilitate real-time data analysis, enabling organizations to align their quality practices with dynamic market demands.
One prominent trend is the shift towards automation. Automation in Quality 4.0 streamlines operations, reduces human error, and enhances productivity. By embracing automated quality controls, businesses can ensure compliance with standards while freeing up valuable resources for strategic initiatives. Furthermore, automation fosters agility in responding to changing consumer expectations and technological advancements, which is key in maintaining a competitive edge.
Sustainability also plays a significant role in the future of Quality 4.0. As environmental concerns grow, organizations must implement practices that not only enhance product quality but also minimize their ecological footprint. This alignment of quality and sustainability necessitates the adoption of sustainable materials, efficient waste management systems, and energy-saving technologies. A commitment to sustainability can enhance brand reputation, attract environmentally conscious consumers, and ultimately lead to cost savings through more efficient resource utilization.
Continuous innovation in quality practices is essential in this Digital Age. Businesses must cultivate a culture that promotes ongoing improvement and adaptation, integrating feedback loops and collaborative partnerships into their quality management systems. By leveraging data-driven insights and staying attuned to emerging trends, organizations can envision a future where quality and sustainability coalesce, leading to healthier business models built for long-term success.
Our Message to Our Clients and Partners:
At NA Consultancy, we believe that adopting Industry 4.0 technologies is the key to sustainable growth and excellence. We invite you to explore how these concepts can enhance the quality of your products and services while achieving a strong return on investment.
Share Your Thoughts!
What do you think about transitioning to Quality 4.0? Has your company already started adopting these concepts? We’d love to hear your experiences and ideas in the comments!
Driving Smart Solutions for a Digital Future
contact us
info@naconsultancy.com
+966572439114
+201094167180
keep Updated
Jeddah 23531, Saudi Arabia